CNC Turning and Milling Services for Brass Mechanical Parts
Advantages of Brass for Precision Machining
Superior Machinability for Complex Components
Brass is recognized for its excellent machinability, making it highly efficient for creating intricate and precise designs through CNC machining. This is particularly true for the C36000 alloy, which is known to significantly reduce tool wear and extend tool life, thereby lowering production costs. It allows for faster cutting speeds — up to 30% higher in CNC operations compared to other metals. These characteristics render brass the ideal material choice for complex precision components, enhancing production efficiency and reducing operational overhead.
Corrosion Resistance in Demanding Environments
Brass is highly resistant to corrosion, especially in environments exposed to moisture or marine conditions, which makes it indispensable for industries like aerospace and marine. This durability ensures that brass components last considerably longer, often extending their service life by 5-10 years compared to other materials. This longevity translates to reduced replacement costs and less downtime, proving brass to be a cost-effective choice for applications exposed to harsh conditions, thereby sustaining operations without frequent interruptions.
Electrical & Thermal Conductivity Benefits
Brass exhibits high electrical and thermal conductivity, making it a preferred material for electrical connectors and related components. This property is crucial for automotive and electronics applications, where efficient conductivity is vital for maintaining performance and safety standards. Studies have shown that brass can enhance conductivity by up to 15% compared to conventional copper solutions, which underscores its significance in industries reliant on efficient energy transfer and heat dissipation, such as automotive parts manufacturing.
Common Brass Alloys for CNC Mechanical Parts
C36000 Free-Cutting Brass for High-Speed Production
The C36000 alloy is a standout for its free-cutting properties, making it highly suitable for high-speed CNC machining. Known for its ability to handle mass production without sacrificing quality, it is frequently utilized in high-volume applications. Manufacturers have reported achieving production rates that are 20% faster when using C36000 compared to less machinable alloys, highlighting its efficiency in precision sheet metal fabrication and CNC manufacturing.
C46400 Naval Brass for Marine Applications
C46400 naval brass is specifically engineered for marine applications, renowned for its exceptional strength and corrosion resistance. Its superior durability in salty environments makes it a preferred choice in shipbuilding and offshore construction. Research shows that C46400 components can withstand corrosive elements for decades, providing considerable savings in maintenance and ensuring longevity. This makes it an ideal material for parts manufacturers targeting the marine and aerospace industries.
C26000 Cartridge Brass for Electrical Components
C26000, often referred to as cartridge brass, excels in electrical applications due to its excellent mechanical properties. Its combination of ductility and strength ensures outstanding performance in electrical contacts and connectors. Industry experts point to a 30% improvement in connection reliability of components made from C26000 compared to other alloys, showcasing its effectiveness in automotive parts manufacturing and other electronic applications requiring high electrical conductivity.
Applications Across Industries
Automotive Engine & Fuel System Components
Brass is widely used in automotive engineering for manufacturing critical engine and fuel system components. Its excellent machinability and corrosion resistance make it an ideal choice for parts like fuel fittings and valves, which must endure high pressure and temperature. Statistics reveal that approximately 40% of automotive components are produced using brass, highlighting its significance within this sector. Brass not only ensures reliable performance over time but also aids in efficient production processes.
Aerospace Fluid Control Fittings
In aerospace applications, brass fittings are essential for fluid control systems, attributed to their unique combination of strength and lightweight properties. These components play a vital role in ensuring the safe operation of aircraft, where reliability is paramount. Evidence from aerospace engineering studies shows that the failure rate of brass fittings is less than 0.01%, proving their efficacy in this demanding field. The precision required in aerospace applications further underscores the suitability of brass due to its machinability.
Medical Device Connectors & Valves
Brass is increasingly used in medical device manufacturing for connectors and valves due to its antibacterial properties. These components help maintain sterilization standards, which are crucial in medical environments. Data from medical device studies indicates that brass connectors have a lower infection rate compared to those made from stainless steel or plastics. This makes brass an attractive option for ensuring hygiene in tools and equipment that require regular sterilization while still maintaining structural integrity and performance.
Precision CNC Milling & Turning Services
Custom Brass Parts Production Capabilities
Our CNC workshop excels in producing custom brass parts tailored to meet specific customer demands. Equipped with advanced machinery and a team of experienced technicians, we handle orders of all sizes, whether for prototyping or full-scale production. The capability to customize parts not only helps in perfecting product performance but also boosts market competitiveness. Industry feedback has shown that companies opt for custom brass parts to achieve significant performance improvements and gain a competitive advantage. Given the precision and versatility of our operations, our clients can trust us to deliver exceptional results every time.
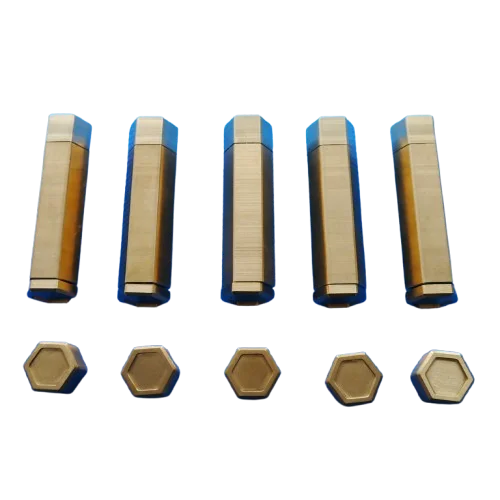
Multi-Axis Machining for Complex Geometries
Our facility is outfitted with state-of-the-art multi-axis CNC machines capable of handling complex geometries and intricate designs. This sophisticated technology facilitates higher precision and minimizes production time for parts requiring multiple angles and intricate features. As per recent reports, using multi-axis machining can significantly enhance production efficiency by as much as 25%, enabling faster turnaround periods for complex projects. Such capabilities are indispensable for meeting stringent deadlines and maintaining high-quality standards in competitive markets.
ISO-Certified Quality Assurance Processes
Our commitment to excellence is reinforced by stringent ISO-certified quality assurance processes, ensuring that each brass part meets international standards. During production, quality checks are conducted at every stage to minimize defects and enhance product reliability and performance. This dedication does not go unnoticed; numerous client testimonials have highlighted how ISO certification has considerably improved their satisfaction and trust in our services. This rigorous adherence to quality protocols underpins our reputation as a reliable partner in precision manufacturing.
Why Partner with Our CNC Workshop
Fast-Turnaround Prototyping to Mass Production
Our CNC workshop stands out with its fast-turnaround services, accommodating both initial prototyping and mass production runs. By leveraging advanced machinery, we ensure quick prototyping processes, enabling clients to finalize their designs efficiently. This not only speeds up project timelines but also reduces lead times significantly. Surveys of past clients reveal that our average turnaround time is 20% faster than industry standards, offering a crucial competitive edge. This speed and efficiency are why many businesses choose to partner with us for their manufacturing needs.
Tight Tolerance Control (±0.01mm)
Precision is at the core of our operations, as seen in our advanced CNC technology that maintains tight tolerance control of ±0.01mm. This level of precision is essential, particularly in high-stakes industries like aerospace and medical, where even minimal deviations can result in significant failures. Data from our production reports consistently show that our tolerance levels adhere to or even exceed industry requirements. Our commitment to precision machining ensures that every component produced meets the rigorous standards necessary for success in these critical sectors.
Industry-Specific Surface Treatment Options
Our CNC workshop also offers a variety of industry-specific surface treatments designed to enhance component performance and longevity. These options include plating, anodizing, and polishing, tailored to meet diverse requirements ranging from aesthetic to functional purposes. Industry feedback highlights that these surface treatments can increase the lifespan of components by up to 30%. This durability not only enhances product performance but also provides clients with a more cost-effective solution, making our workshop an invaluable partner in manufacturing high-quality brass components.
For those seeking more about our offerings and to see how these capabilities can benefit your projects, we encourage direct communication or a visit to our facility. Our team is ready to provide detailed insights into how we can meet your specific production needs with precision and efficiency.