The Importance of Precision in CNC Machined Parts
Defining Precision in CNC Machined Parts
Understanding CNC Machining Tolerances
CNC machining tolerances are the allowable deviations from specified measurements, crucial for ensuring the functionality and compatibility of machined parts. These tolerances dictate how much a part can vary from its nominal size while still remaining functional, which is vital in industries such as aerospace, medical, and automotive parts manufacturing. Industries adhere to stringent standards, such as ISO or ASME, to maintain these tolerances and ensure quality control. CNC technology can achieve impressive tolerances as tight as ±0.001 inches, contingent on materials and design complexity. Understanding these standards aids in improving production efficiency, reducing errors, and ensuring consistent quality across large-scale manufacturing processes.
Role of CAD/CAM in Precision Engineering
CAD (Computer-Aided Design) and CAM (Computer-Aided Manufacturing) systems have revolutionized precision engineering by enabling highly accurate design and production processes. These tools allow engineers to simulate, visualize, and rectify design issues before manufacturing, significantly reducing errors. The integration of CAD/CAM can decrease production time by up to 30%, leading to enhanced manufacturing efficiency. Modern software includes advanced features for optimizing machining parameters, crucial for achieving tight tolerances required in precision sheet metal fabrication. By leveraging these technologies, manufacturers ensure consistent and reliable CNC machining outputs, thus enhancing the overall quality and precision of fabricated components.
Key Industries Relying on Precision CNC Machining
Aerospace & Defense: Demanding Zero-Failure Components
The aerospace and defense industries are inherently demanding, requiring components that adhere to strict regulations and zero-failure criteria. Precision CNC machining plays a pivotal role in ensuring these parts can withstand extreme conditions, such as vast fluctuations in pressure and temperature seen in flight or ground operations. The advancement in the aerospace sector is a testament to the benefits of precision machining. This technique contributes significantly to the safe and efficient operation of aircraft, crucially in components like turbine parts, structural elements, and critical fasteners. These components rely heavily on high precision, cementing CNC machining's role in their production.
Medical Device Manufacturing: Life-Saving Accuracy
In medical device manufacturing, precision is not just vital—it is life-saving. The components crafted through CNC machining, such as surgical instruments and implants, must meet stringent quality and accuracy standards to ensure functionality and patient safety. The FDA mandates rigorous testing and documentation, emphasizing precision in this industry to avert any possible failures. CNC machining provides the high precision necessary to produce medical devices capable of saving lives and improving patient outcomes, reinforcing the critical nature of accuracy in this field.
Automotive & Sheet Metal Fabrication Applications
Automotive manufacturing significantly relies on precision CNC machining for pivotal components such as engine blocks, transmissions, and structural elements. Precision sheet metal fabrication, equally vital, contributes to creating lightweight yet robust parts required by modern vehicles. Automotive industry standards often require tolerances within ±0.005 inches to ensure the optimal performance of its components. Technological innovations in CNC machining have made it possible to mass-produce these precision parts, playing a vital role in enhancing vehicle efficiency and safety, especially as the industry moves towards electric vehicles and lightweight materials.
Technological Advancements Driving CNC Precision
5-Axis Machining for Complex Geometries
The incorporation of 5-axis machining has revolutionized CNC machining by allowing the creation of complex geometries previously impossible with traditional 3-axis milling. Unlike its predecessor, a 5-axis CNC machine can move the cutting tool along five different axes simultaneously, leading to enhanced machining accuracy and efficiency. This technology not only reduces the need for multiple setups but also improves surface finishes and achieves tighter tolerances. Key industries benefiting from this advancement include aerospace, automotive, and medical device manufacturing, where intricate parts require high precision. According to recent industry reports, manufacturers leveraging 5-axis technology have noted significant improvements in their production processes.
Integration of AI for Error Reduction
In recent years, Artificial Intelligence (AI) integration into CNC machining has become pivotal for error reduction and process optimization. AI algorithms are designed to analyze data from ongoing machining processes to predict and mitigate potential errors in real-time. Companies that have adopted AI-driven solutions report a notable 25% reduction in scrap rates and marked improvements in operational efficiency. This integration facilitates not only cost reduction but also accelerates production cycles while maintaining high precision standards. The success of AI in CNC machining underscores the importance of adapting technological advancements to maintain competitiveness in modern manufacturing landscapes.
Rapid Prototyping Services & Iterative Refinement
Rapid prototyping services have significantly impacted the manufacturing landscape by enabling quick testing and validation of designs. Through CNC machining, manufacturers can iteratively refine prototypes, ensuring they meet precise specifications before final production. This capability is key in reducing the time to market by up to 50%, offering companies a substantial competitive advantage. By addressing design flaws early in the development cycle, manufacturers can ensure higher quality final products. The role of CNC machining in rapid prototyping highlights its importance in innovation, providing both flexibility and precision in modern product development processes.
Benefits of High-Precision CNC Machining
Reduced Material Waste Through Exact Tolerances
Precision CNC machining plays a pivotal role in minimizing material waste by achieving exact tolerances during production. This technological advancement is essential for sustainability initiatives across industries, as it efficiently reduces excess material. Industries adopting precision machining often report waste reductions of up to 30%, which not only enhances cost-effectiveness but also supports environmental goals. By ensuring that each component is crafted with precision, manufacturers can avoid unnecessary material removal, fostering a greener production approach.
Cost Efficiency in Mass Production
High-precision CNC machining offers significant cost efficiencies, particularly in mass production scenarios. The technology decreases material wastage and reduces machining time, contributing to lowered production costs. Maintaining high quality while increasing output is immensely beneficial, as evidenced by companies reporting a 20% cost saving in operations after transitioning to high-precision CNC processes. This improvement ultimately leads to a better return on investment (ROI) for manufacturers, as resources are optimized, allowing for increased profitability and scalability.
Enhanced Product Reliability Across Sectors
Precision CNC machined parts are crucial for ensuring the reliability of products across various applications. The use of accurately machined components leads to improved product reliability, resulting in fewer maintenance requirements and heightened customer satisfaction. Industries utilizing high-precision components have reported a significant decrease in product failures. This enhancement in reliability supports brand reputation and encourages repeat business, as customers can trust the consistent quality and performance of products manufactured using precision machining processes.
Precision CNC Machined Parts in Industrial Applications
Custom Extruded Aluminum Profiles for Structural Integrity
Custom extruded aluminum profiles are essential in maintaining structural integrity in various architectural and industrial applications. With the help of precision CNC machining, these profiles can be tailored to meet specific design and performance criteria. This customization ensures that aluminum sections are lightweight solutions without sacrificing durability, making them suitable for numerous sectors. Custom Extruded Aluminum Profiles crafted by precision CNC machining offer unmatched detail and structural support, ensuring that every project meets exacting standards.
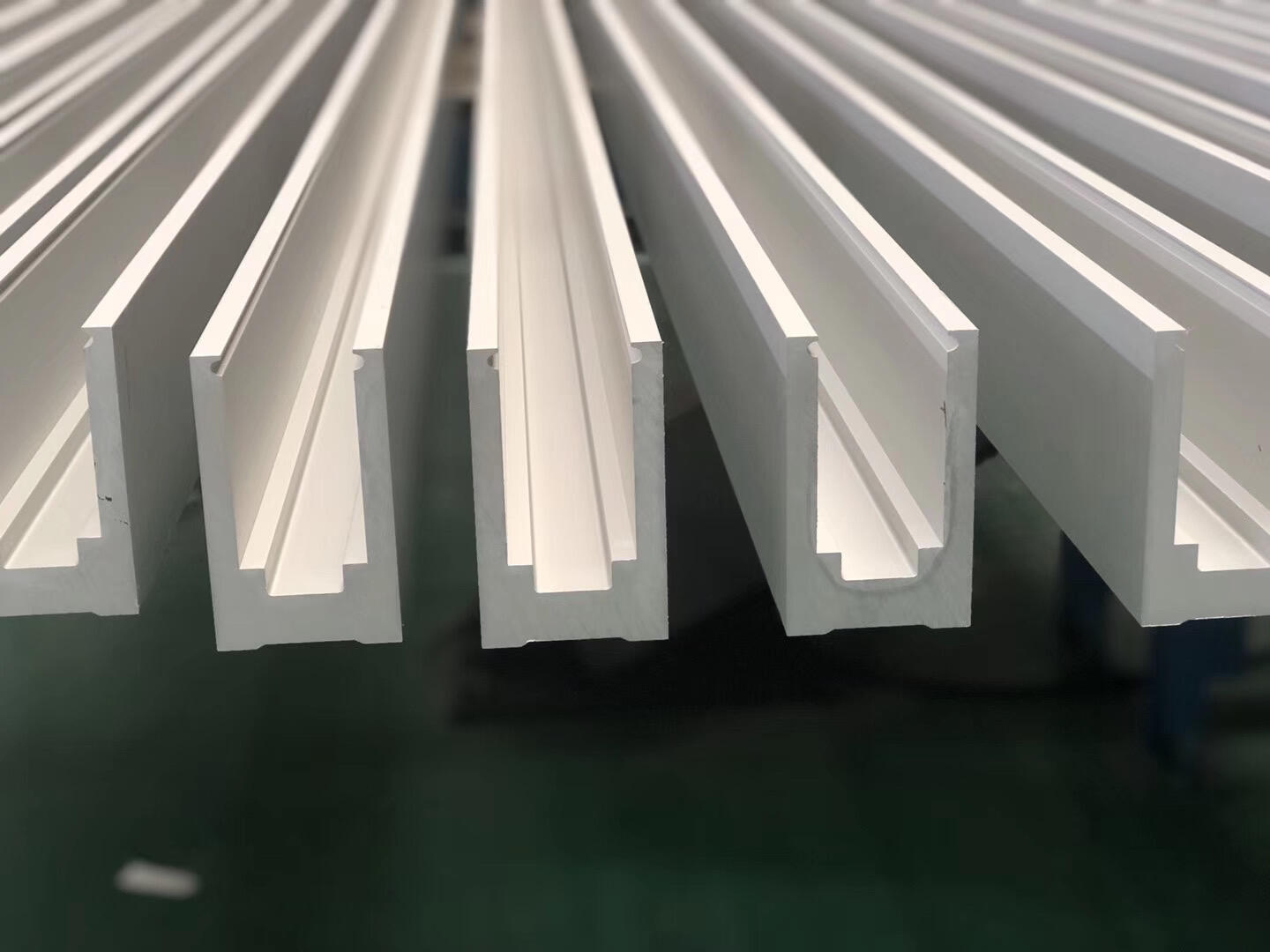
Wireless Infrastructure Components for 5G Networks
The advent and expansion of 5G networks necessitate precise components capable of managing increased data transmission demands. CNC machining is instrumental in creating components such as antennas and connectors with the precision required for enhanced data throughput and connectivity. The standards set by 5G technology have escalated the precision requirements in manufacturing these essential infrastructure components. For instance, 150 Sets Precision CNC Machined Parts have proven crucial in maintaining the performance and reliability of wireless communications infrastructure, showcasing the indispensable role of precision machining in the evolution of network technologies.
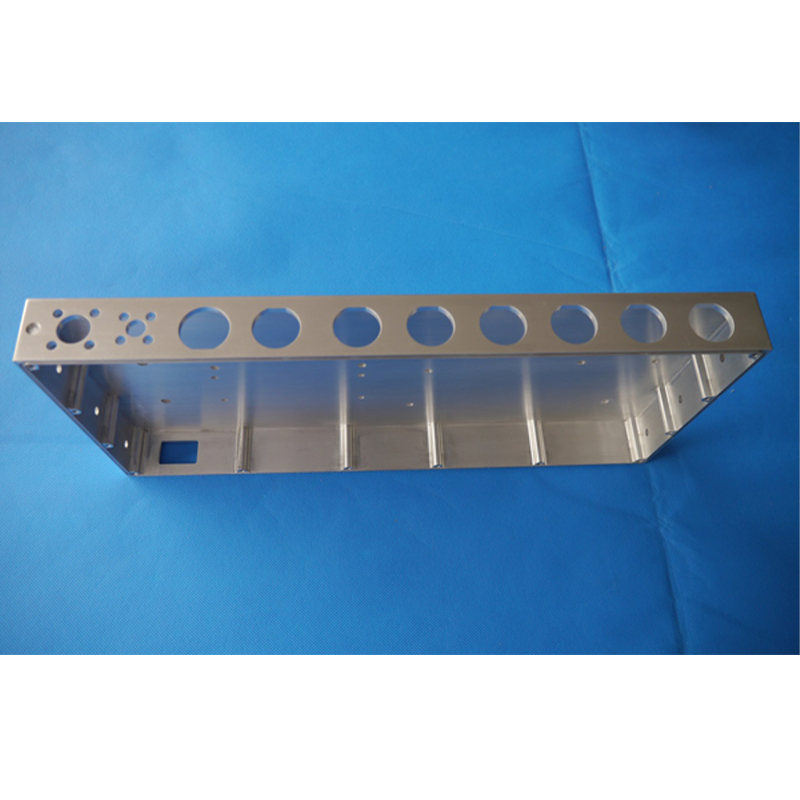
Aerospace-Grade Electronic Instrumentation Parts
In the aerospace sector, precision is paramount, especially when it comes to electronic instrumentation parts. Even the smallest deviations can lead to significant consequences in terms of safety and functionality. CNC machining ensures the production of parts that meet stringent aerospace standards, reinforcing their crucial role in maintaining reliability and performance. For example, the 180 Sets of Precision CNC Machined Parts serve aerospace applications with an unmatched level of precision, thereby guaranteeing the reliability and safety of aircraft systems.
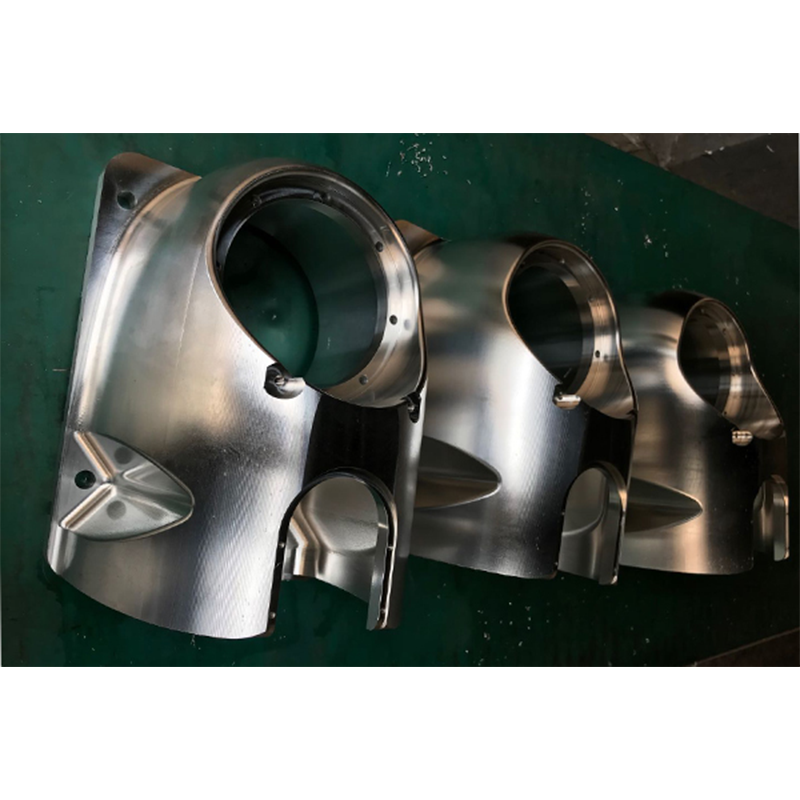
High-Performance Heat Sinks for Thermal Management
Heat sinks are pivotal in managing thermal regulation in electronic applications, ensuring that systems remain cool and functional under varying conditions. High-performance heat sinks produced through precision CNC machining achieve optimal fits and maximize cooling capabilities. The efficiency of these components directly correlates with system reliability, making precision machining essential. The 100 Sets Aluminum 6061 Precision CNC Machined Heat Sink exemplify how CNC precision contributes to superior thermal management solutions.
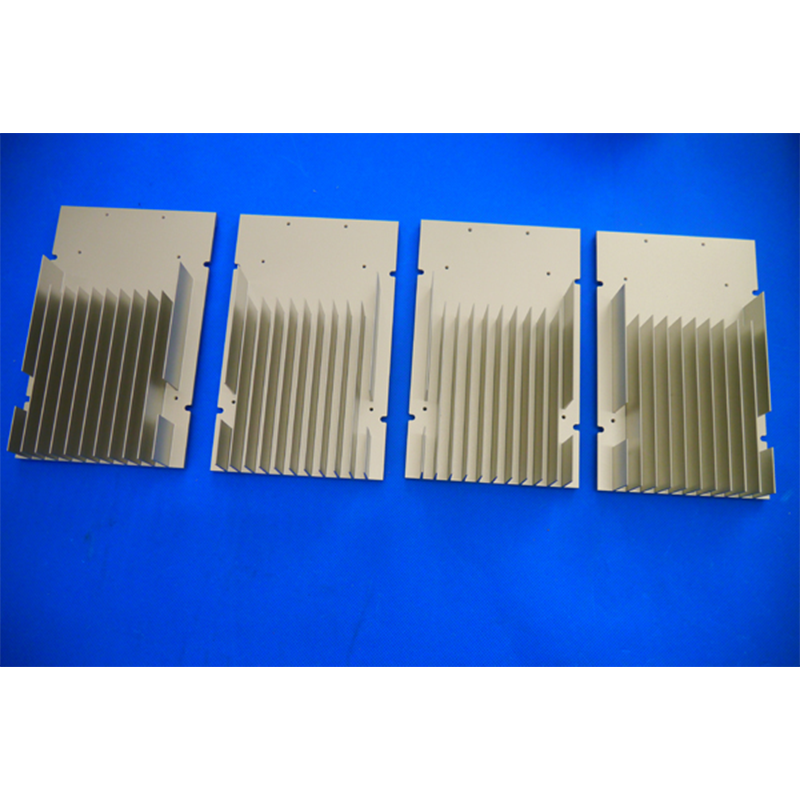
Hydraulic Power Systems with Tight Tolerance Requirements
Hydraulic power systems rely on components produced with strict tolerance specifications to ensure performance and reliability. CNC machining plays a critical role in manufacturing parts that uphold leak-free and efficient hydraulic operations. Precision in these systems directly impacts energy efficiency and operational capabilities. The 12 Sets Precision CNC Machined Parts demonstrate the essential nature of CNC precision in crafting parts that meet the rigorous demands of hydraulic systems.
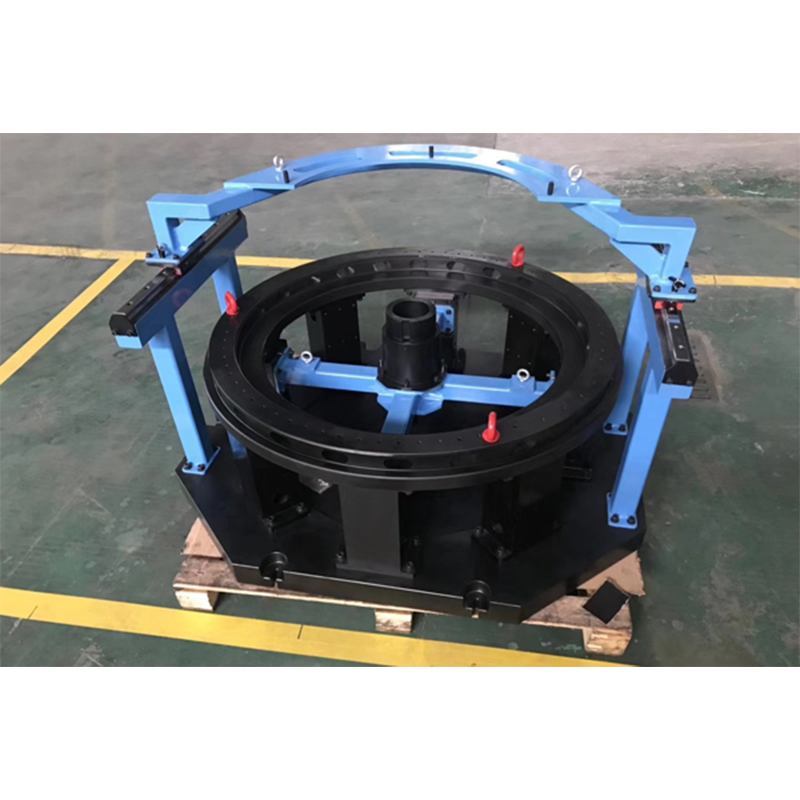
Ensuring Quality in CNC Machined Components
ISO Certification & Compliance Standards
ISO certification offers a robust framework crucial for quality management in CNC machining, ensuring compliance and standardization in processes. By adhering to these international standards, companies not only boost their credibility but also reassure clients of reliable and consistent production outputs. Notably, organizations that achieve ISO certification enjoy greater customer trust and face lower operational risks. This widely recognized certification is a testament to a company’s dedication to maintaining high quality throughout its production stages, resulting in products that meet stringent industry benchmarks.
Advanced Metrology Tools for Precision Verification
Employing advanced metrology tools is critical for manufacturers intent on achieving precision verification in CNC machining. Tools like coordinate measuring machines (CMM), optical scanners, and laser measuring devices play a pivotal role in ensuring components meet exact tolerances. These sophisticated instruments provide accurate measurements, significantly reducing the incidence of defects in machined parts. Consequently, metrology tools are indispensable in supporting the production of higher quality outputs, aligning with the demands of industries that require stringent accuracy and reliability in their components.