Vantaggi della lavorazione CNC personalizzata per la produzione di parti complesse
Comprensione della lavorazione CNC personalizzata
La lavorazione CNC (Computer Numerical Control) personalizzata è un processo di produzione che utilizza la tecnologia informatica per realizzare componenti precisi adatti alle specifiche esigenze del cliente. Integrando una tecnologia CNC avanzata, le aziende possono creare parti complesse con alta precisione, adattandosi a progetti e specifiche unici. Questo processo versatile è fondamentale in vari settori, come l'automotivo, l'aerospaziale e il medico, dove precisione e personalizzazione sono essenziali.
L'evoluzione della fresatura CNC dagli metodi manuali a sistemi basati su computer sofisticati segna un cambiamento significativo nel panorama della manifattura. Inizialmente, le macchine erano operate manualmente, il che era tempo consumante e spesso inesatto. Tuttavia, l'introduzione della tecnologia CNC ha portato miglioramenti sostanziali. Oggi, i sistemi CNC sono dotati di funzionalità avanzate come capacità multi-asse e processi automatizzati, migliorando notevolmente l'efficienza e la precisione. Secondo statistiche del settore, il mercato della fresatura CNC è destinato a crescere a un tasso di crescita annuo composto (CAGR) del 6,3% dal 2020 al 2028, sottolineando l'aumento della domanda e della dipendenza da queste tecniche di produzione avanzate.
Vantaggi della Fresatura CNC Personalizzata
La lavorazione CNC personalizzata offre una precisione e accuratezza straordinarie nella produzione, raggiungendo livelli di tolleranza stretti e percentuali di accuratezza elevate. Gli esperti attestano che la lavorazione CNC può mantenere tolleranze entro ±0,01 pollici (±0,127 mm), mentre i sistemi avanzati possono raggiungere tolleranze fino a ±0,0005 pollici (±0,0127 mm). Per esempio, ingegneri meccanici come Andrew Willing sottolineano la precisione della lavorazione CNC nella produzione di parti complesse, consentendo un'integrazione senza soluzione di continuità in assemblee più grandi. Questa precisione non solo garantisce la coerenza e la qualità di ogni componente, ma consente anche progetti complessi e dettagliati senza compromettere l'accuratezza.
La versatilità della fresatura CNC si estende attraverso molteplici industrie, ciascuna delle quali trae beneficio dalla sua capacità di fornire soluzioni personalizzate. Nell'industria automobilistica, la tecnologia CNC viene utilizzata per produrre componenti come parti del motore e telaio, garantendo che ciascuno rispetti standard rigorosi di sicurezza e prestazioni. Nell'aerospaziale, la produzione di componenti leggeri e resistenti è fondamentale, e la fresatura CNC fornisce un'accuratezza senza pari. Il campo medico conta sulla fresatura CNC per creare componenti complessi per strumenti chirurgici e impianti adatti alle esigenze specifiche dei pazienti. Accogliendo una vasta gamma di materiali e geometrie complesse, la fresatura CNC rappresenta un bene indispensabile in questi settori e oltre, sottolineando il suo ruolo inestimabile nella manifattura moderna.
Principali applicazioni della fresatura CNC su misura
Applicazioni nell'industria aerospaziale
La lavorazione CNC personalizzata ha rivoluzionato l'industria aerospaziale, offrendo una precisione senza pari per componenti critici come i supporti e i pezzi del motore degli aerei. Questa precisione è fondamentale per garantire sicurezza ed efficienza nelle operazioni aerospaziali. Negli ultimi anni, la richiesta di componenti realizzati con tecnologia CNC in questo settore è aumentata notevolmente, con dati che mostrano un tasso di crescita annuale significativo. Questo aumento è principalmente dovuto alla capacità della lavorazione CNC di rispettare le tolleranze strette richieste per le applicazioni aerospaziali, migliorando così le prestazioni e la sicurezza complessiva degli aerei.
Produzione di Dispositivi Medici
La lavorazione CNC svolge un ruolo fondamentale nella produzione di dispositivi medici, consentendo la creazione di strumenti e impianti precisi. Il processo garantisce il rispetto dei rigidi standard normativi, fondamentali nel campo medico. I componenti medici realizzati con tecnologia CNC, come arti protesici e strumenti chirurgici, devono superare controlli di qualità rigorosi per garantire la sicurezza del paziente ed efficacia. Grazie ai progressi nella tecnologia CNC, la capacità di produrre dispositivi medici complessi e personalizzati si è migliorata, permettendo una migliore assistenza sanitaria personalizzata.
Produzione di componenti automobilistici
Nell'industria automobilistica, la lavorazione CNC su misura è essenziale per la produzione di componenti precisi come parti del motore, cassette del cambio e sistemi di sospensione. La tecnologia CNC consente una precisione e ripetibilità elevate, fondamentali per le prestazioni e la durata dei componenti automobilistici. Man mano che l'industria automobilistica si muove verso veicoli sempre più elettrici e autonomi, la lavorazione CNC continua ad adattarsi, incorporando materiali e tecnologie avanzate per affrontare nuove sfide. Innovazioni come la produzione ibrida integrata CNC sono destinate a ottimizzare ulteriormente i processi produttivi, riducendo i costi e aumentando l'efficienza nella produzione automobilistica.
Prodotto in evidenza: Componenti CNC lavorati con alta precisione
I vantaggi di un'alta precisione nel fresamento CNC personalizzato in fabbrica, specialmente per i componenti in lega di alluminio con cavità, sono numerosi. Questi componenti sono progettati specificamente per settori che richiedono alta accuratezza ed efficienza, come l'elettronica e l'aerospaziale. La personalizzazione consente requisiti specifici di forma e dimensione, migliorando la loro efficacia in ambienti complessi.

L'elaborazione e la produzione di componenti meccanici CNC in ottone per tornitura offrono capacità di personalizzazione avanzate essenziali per varie applicazioni industriali. Questi componenti sono ideali per settori che richiedono componenti meccanici precisi come connettori e giunti, consentendo modifiche specifiche in base alle diverse esigenze industriali.
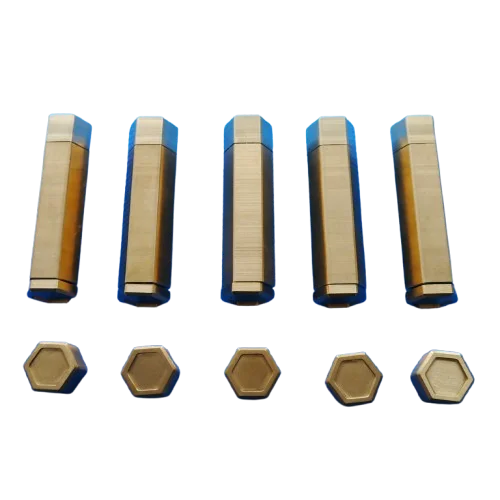
La lavorazione CNC ad alta precisione di radiatori in lega di alluminio offre una grande flessibilità di progettazione e un miglioramento delle prestazioni per i fornitori. Questa tecnica consente ai produttori di adattare le specifiche dei radiatori per superare le aspettative di prestazioni di raffreddamento standard in ambienti elettronici e automobilistici impegnativi.
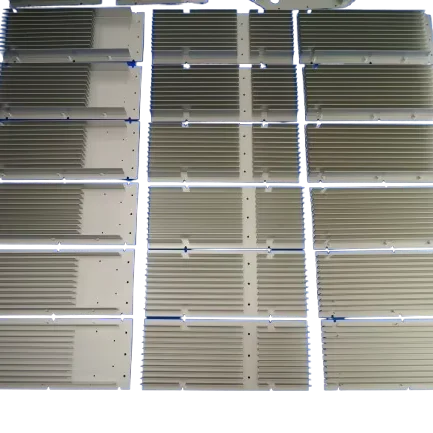
La lavorazione su misura OEM utilizzando la macchinazione CNC a cinque assi è fondamentale per la produzione di componenti automobilistici complessi con precisione e scalabilità elevate. Questo metodo garantisce una riproduzione di alta qualità di geometrie complesse e migliora i tempi di produzione, mantenendo gli standard esatti necessari per le applicazioni automobilistiche.
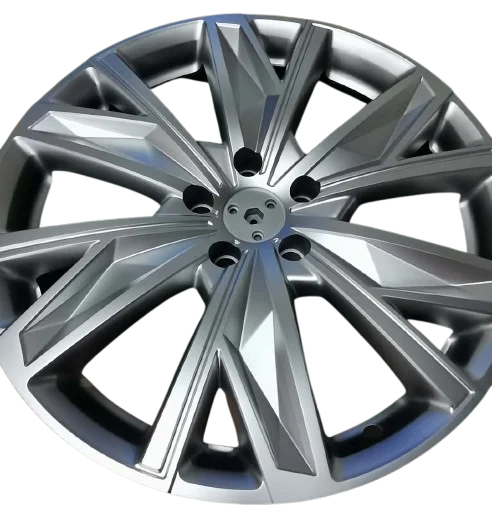
Come scegliere un servizio di lavorazione CNC personalizzato
Scegliere un servizio di fresatura CNC affidabile richiede la valutazione di fattori chiave come la tecnologia che utilizzano, l'esperienza della loro forza lavoro e i tipi di macchine CNC che offrono. Macchinari avanzati come il fresamento CNC a 5 assi e i centri di tornitura complessi possono gestire progetti intricati e tolleranze strette, il che è fondamentale per la produzione di componenti precisi. Inoltre, una manodopera qualificata garantisce che i progetti vengano interpretati correttamente e che le migliori pratiche di lavorazione vengano applicate per efficienza e qualità.
Comprendere i costi di produzione e i tempi di consegna è fondamentale quando si sceglie un servizio di fresatura CNC. È importante analizzare accuratamente le offerte, il che significa capire il rapporto tra la complessità del progetto, i materiali utilizzati e le velocità di lavorazione. Progetti più complessi o materiali speciali potrebbero aumentare i costi e prolungare i tempi di consegna. Quindi, quando si valutano le offerte, bisogna considerare non solo il prezzo, ma anche come questi fattori influenzino la tabella di marcia complessiva della produzione e l'efficienza del costo finale.
Future Trends in Custom CNC Machining
L'integrazione dell'automazione e dell'intelligenza artificiale (IA) nella lavorazione CNC su misura sta trasformando rapidamente l'industria. Grazie all'inserimento di tecnologie IA, i tornitori possono beneficiare di una precisione migliorata e di un riduzione degli errori umani, semplificando notevolmente i processi produttivi. Ad esempio, gli algoritmi AI possono ottimizzare i percorsi degli strumenti e i modelli di taglio, portando a un utilizzo efficiente dei materiali e a un diminuzione del tempo di produzione. Inoltre, l'automazione consente alle macchine di eseguire compiti complessi in modo autonomo, migliorando l'efficienza operativa e permettendo alle aziende di scalare la produzione senza un aumento proporzionale dei costi del lavoro.
La sostenibilità sta diventando un focus centrale dell'industria della lavorazione CNC, con le aziende che adottano sempre più pratiche eco-friendly per ridurre il loro impatto ambientale. Tecniche di riduzione dei rifiuti, come il riciclo delle schegge metalliche e l'ottimizzazione dei tagli dei materiali, vengono implementate per migliorare l'efficienza materiale. Ad esempio, aziende come Siemens e Bosch stanno introducendo pratiche CNC sostenibili utilizzando sistemi a ciclo chiuso per il riutilizzo dei materiali. Tali pratiche sostenibili non solo riducono l'impatto ambientale, ma posizionano anche le imprese come leader in un mercato che valuta sempre di più le soluzioni di produzione verdi.